As the construction and infrastructure sectors continue to expand, the demand for efficient cement handling at ports has become increasingly crucial. One of the key solutions enabling safe and effective cement transfer from ships to shore is the
cement ship unloader - a specialized system designed to discharge dry bulk cement quickly, cleanly, and reliably.
If you're new to this field, this guide will walk you through everything you need to know: from the core concept and working principles to types of equipment and real-world applications at modern cement terminals.
What is a cement ship unloading system?
A
cement ship unloading system is a combination of specialized equipment used to unload dry bulk cement from ships or barges at marine ports. These systems are commonly used at
cement import terminals to transfer cement from vessel holds to storage silos or hoppers via enclosed conveying systems.
The equipment is specifically engineered for handling
dry bulk materials, minimizing dust emissions while ensuring high-capacity, safe operation. In countries like Vietnam and throughout Southeast Asia, such systems are widely adopted to support large-scale
cement logistics operations and modern
port cement infrastructure.
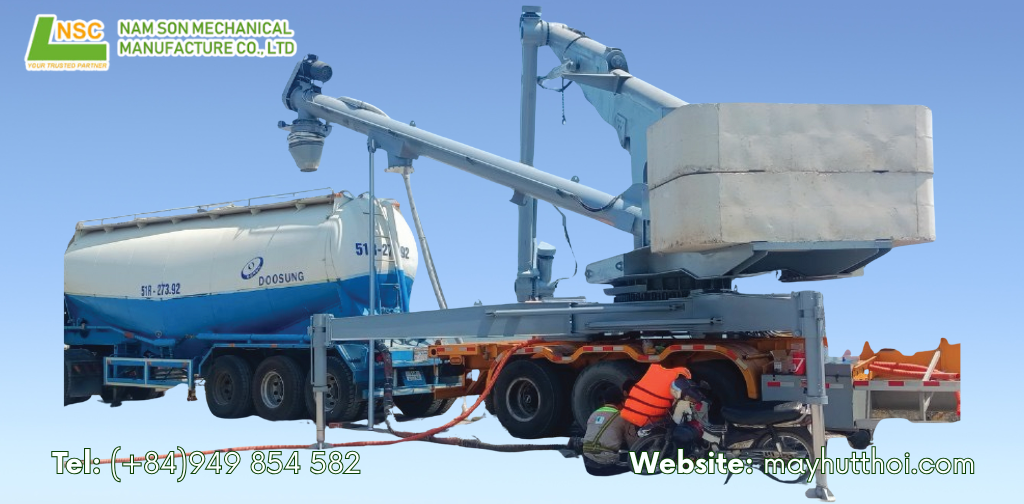
Basic components and how they work
A cement ship unloading system is a combination of key components designed to transfer bulk cement from a vessel’s hold to onshore storage efficiently and cleanly. While there are variations depending on equipment type and port layout, most systems include four essential parts: an intake device, a conveying system, a dust control unit, and a discharge mechanism.
The unloading process begins with a
suction arm or hose, which is inserted into the ship’s cargo hold to draw cement powder. In mechanical systems, this intake might be a scoop or hopper feeding into a
screw conveyor or
bucket elevator. The choice of intake depends on the conveying technology used.
There are two main types of conveying systems:
+ Pneumatic systems use compressed air or vacuum pressure to transport cement through sealed pipelines. These systems are enclosed and dust-free, making them ideal for ports with strict environmental regulations.
+ Mechanical systems use moving components such as screws, chains, or buckets to physically transfer cement. They can offer higher throughput but typically require more maintenance due to mechanical wear.
To ensure clean handling, a
dust collector is integrated into the system. It captures fine particles during transfer, helping the entire operation remain compliant with air quality standards. This feature is particularly critical when dealing with fine cement powders that can easily become airborne.
The final stage is the
discharge system, where cement is transferred into silos or other storage facilities onshore. Discharge points often include flow control valves, airlocks (in pneumatic systems), and level sensors to monitor filling and avoid material loss.
Depending on the setup, the entire unloader can be installed
onboard the ship (for self-discharging vessels) or
on the dockside (as a fixed or mobile unit). In either case, the goal is the same: to move cement from ship to shore in the most efficient, dust-free way possible.
Popular types of cement ship unloading
Choosing the right system depends on vessel size, unloading speed requirements, and site conditions. The most common types include:
○
Pneumatic cement unloader: Ideal for clean, dust-controlled operations. These systems are prevalent in modern
bulk cement terminals for their high efficiency and automation.
○
Screw-type unloader: A type of
mechanical ship unloader using a rotating auger to carry cement upward. Robust but may require more frequent maintenance.
○
Bucket elevator system: Lifts material vertically using rotating buckets. Suitable for high-volume
dry bulk handling systems.
Each type has unique advantages and should be selected based on specific project needs, space constraints, and terminal setup.
=>>> SEE MORE: Choosing the right cement ship unloading system in Vietnam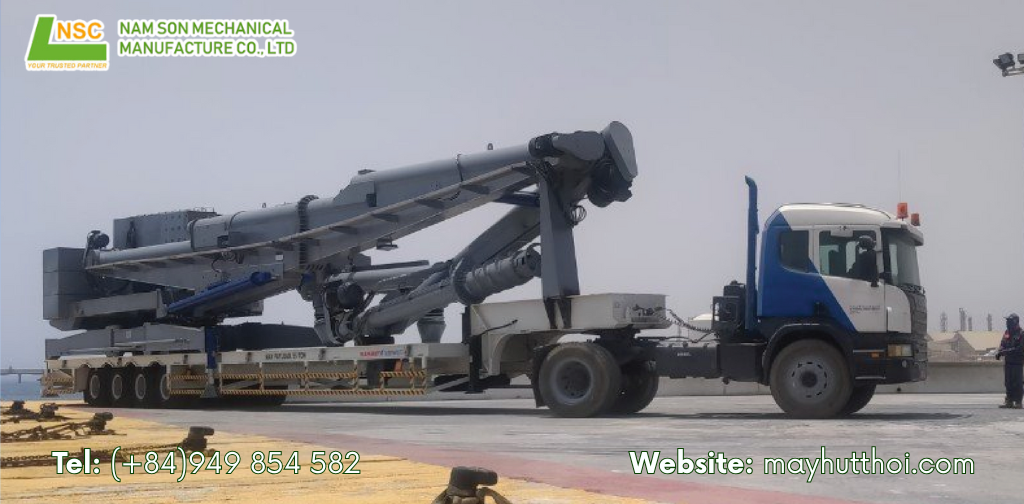
Benefits of using a cement ship unloading system
When properly selected and operated, a cement ship unloader offers clear benefits:
◉ Time efficiency: Systems can achieve unloading rates of 200–300 tons/hour, significantly reducing port turnaround time.
◉ Dust control: Especially in pneumatic conveying systems, the enclosed design ensures low-dust operation, protecting both workers and the environment.
◉ Energy savings: Modern unloaders are engineered for energy-efficient bulk unloading, often with smart automation systems.
◉ Flexible implementation: Available in mobile, modular, or stationary designs, suitable for ports of all sizes.
Additionally, these systems often feature
wear-resistant components, long service life, and reduced labor requirements.
Where are cement ship unloading system used?
Cement unloading systems are widely used in:
+ Cement terminals in Vietnam, Thailand, and the Philippines—handling imports of cement or clinker.
+ Cement plants near coastlinesuse unloaders to receive materials directly from ships.
+ Dry bulk port facilities are connected to inland distribution networks via silos or pipelines.
With Vietnam developing more
specialized cement ports, investing in unloading equipment is now a strategic move for both efficiency and competitiveness.
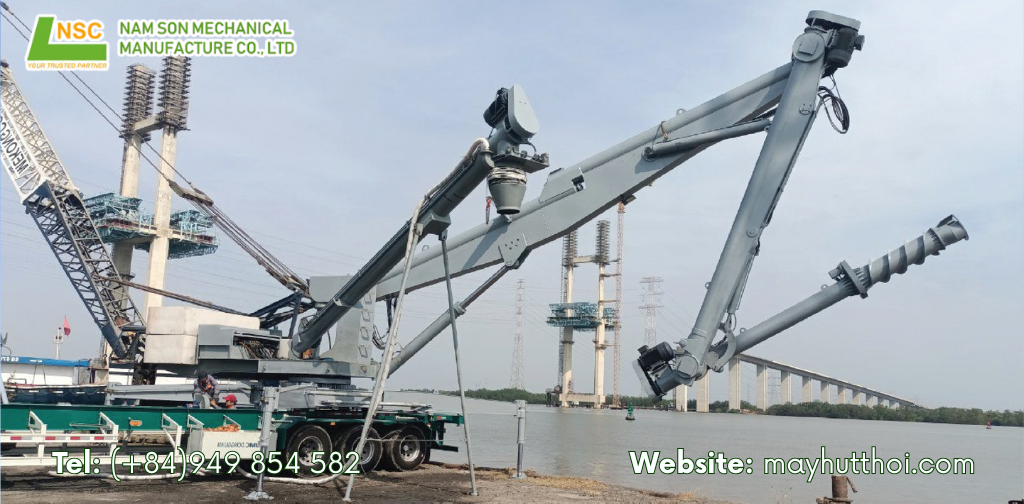
Basic operation & Maintenance for beginners
For those new to cement unloading systems, these basic practices ensure long-term reliability:
- Routine inspections: Check hoses, couplings, and filters for wear or damage.
- Pipeline cleaning: Prevent blockages and maintain air pressure flow in pneumatic lines.
- Calibrate airflow: For pneumatic systems, maintaining optimal pressure ensures smooth operation.
- Dust collector maintenance: Essential for both health and safety and compliance with regulations.
Many modern systems feature
automated controls and sensors, allowing real-time monitoring and error detection.
Industry trends and innovations
The cement handling industry is rapidly evolving, with trends such as:
·Smart unloading controls: IoT-enabled systems for live performance tracking and remote diagnostics.
· Modular and mobile units: Quick installation and relocation options for growing or temporary terminals.
· Sustainable designs: Emphasis on low emissions, noise reduction, and eco-compliance.
As demand for cleaner, smarter, and faster unloading grows,
modern cement ship unloaders are becoming indispensable assets for any terminal.
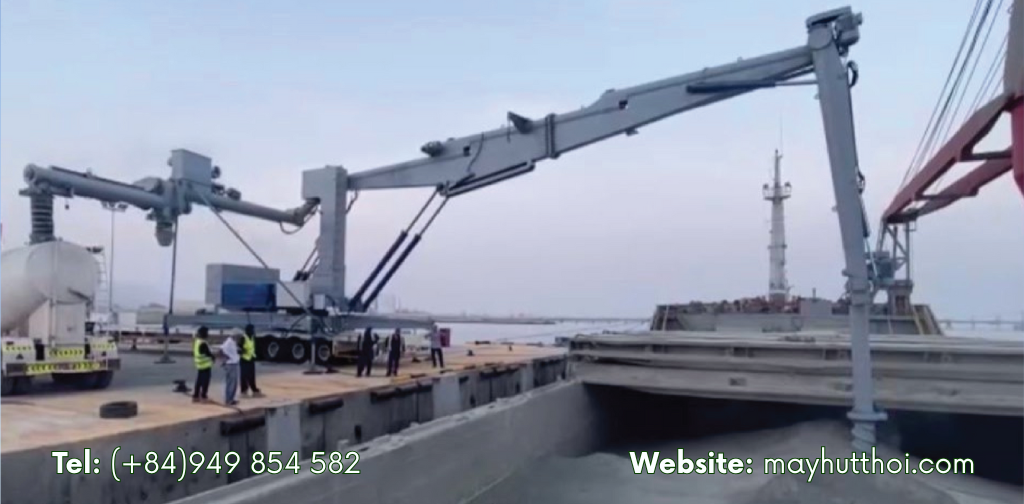
Conclusion
Whether you're an investor, port engineer, or just getting started in cement logistics, understanding how a
cement ship unloading system works is the first step toward making informed decisions.
Investing in the right system not only boosts operational efficiency but also supports safer, cleaner, and more sustainable port management. This beginner’s guide is your foundation for navigating the future of cement unloading at sea.
=>> Learn more: Ship unloader for cementCONTACT US
Need help selecting the right cement ship unloader for your port or terminal?
Contact our experts today for tailored solutions.